Danfoss – IMC: a reliable and efficient alternative to servo technology at Huwa
NETHERLANDS: To meet growing demand for pipe repair clamps and modernize the manufacturing process, Huwa International Pipeline Products set out to automate its pickling line.
Pickling is a method of reinforcing welded joints in steel products where the metal is immersed in a bath of nitric acid and then cleaned. The pickling line employs a biaxial gantry crane that has customarily required servo technology — an expensive and complex solution. By choosing the Danfoss VLT® AutomationDrive FC 302 with its Integrated Motion Controller functionality, Huwa successfully developed a fully automated pickling line with optimum reliability at a reasonable price.
Discover how Huwa International Pipeline Products improved worker safety and reduced lead times on its pickling line with Danfoss VLT® AutomationDrive FC 302 and its Integrated Motion Controller (IMC).
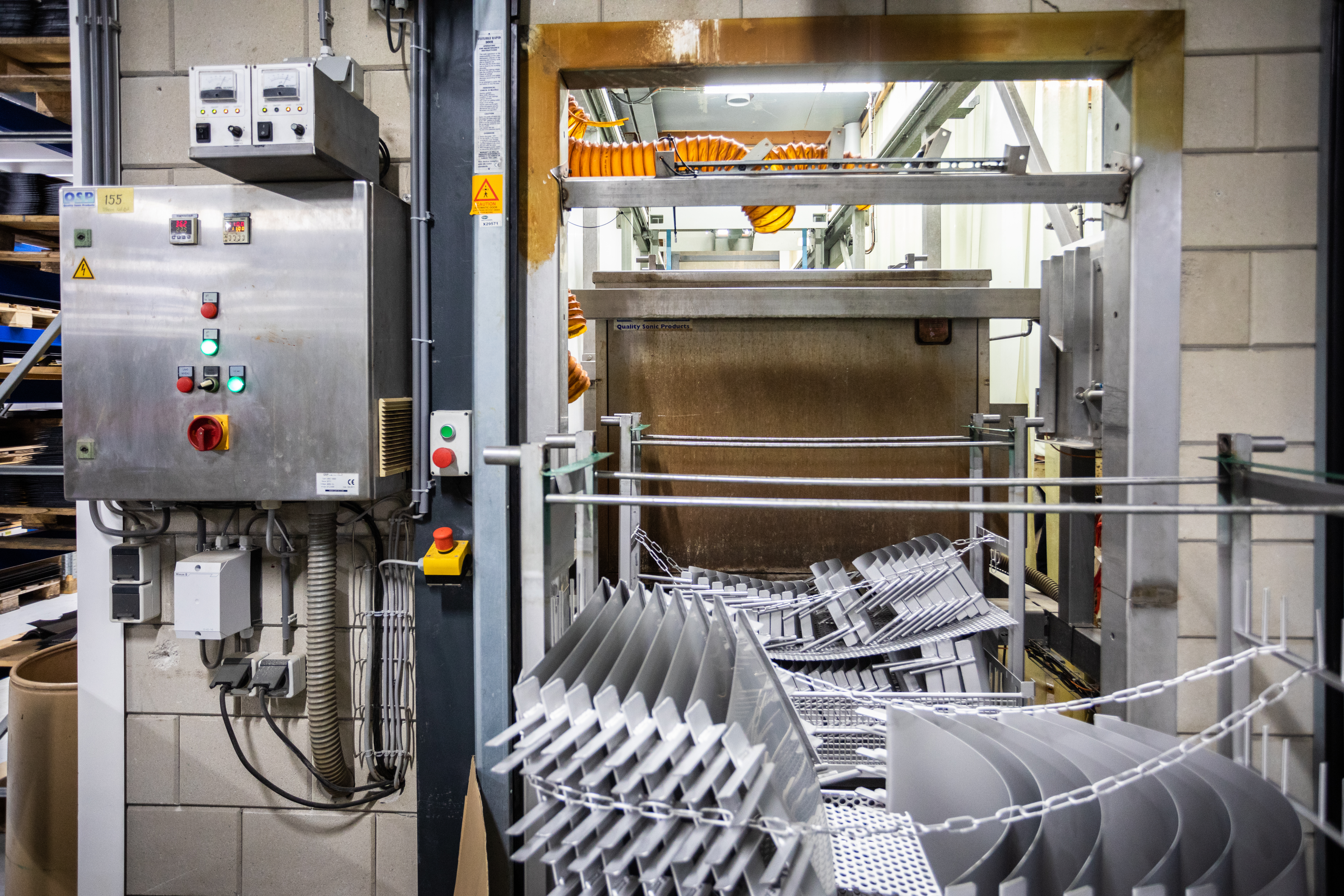
The challenge: Cost-effective precision and reliability
Leaky pipes can lead to a myriad of consequences — commercial to environmental, structural to societal. While replacing a leaky pipe may seem preferable, patching it on site with repair clamps is significantly faster and cheaper.
United Pipeline Products is the largest producer of pipe repair clamps in Europe. The company was formed in 2010 following the merger of six analogous Dutch companies, including Huwa. In fact, United Pipeline Products is one of the world’s leading manufacturers of stainless steel repair clamps. But with increasing global demand for these repair clamps and the use of hazardous chemicals in their production, Huwa decided a change was required in the manufacturing process.
When constructing stainless steel repair clamps, certain parts are welded together, but welding weakens the steel’s properties. To counteract this, clamps are ‘pickled’ —immersed in a bath of nitric acid — and then cleaned. To meet contemporary OH&S standards, Huwa no longer wanted employees to enter the room with the pickling line. Additionally, Huwa hoped to make its pickling line more efficient. The lead time for a basket of parts to be put through the pickling line was two hours, while the process itself took one hour.
The pickling line is a linear setup with four pickling stations, two rinsing steps, an ultrasonic bath and a dryer. To fully automate the process, Huwa needed a drive to control the biaxial gantry crane that hoists baskets of parts in and out of the baths.
With Integrated Motion Controller, you can achieve similar control as with servo technology. You specify the desired speed and position, and the drive subsequently calculates a movement profile and controls the motors. It does this with high repetitive accuracy thanks to feedback with an encoder.
Michael Kannekens, Application Engineer at Danfoss B.V. Netherlands
The solution: VLT® AutomationDrive FC 302 with IMC
In collaboration with local production-line specialists Hellings Machinebouw and electrotechnical supplier Van Egmond, Huwa settled on the VLT® AutomationDrive FC 302 to control the gantry crane.
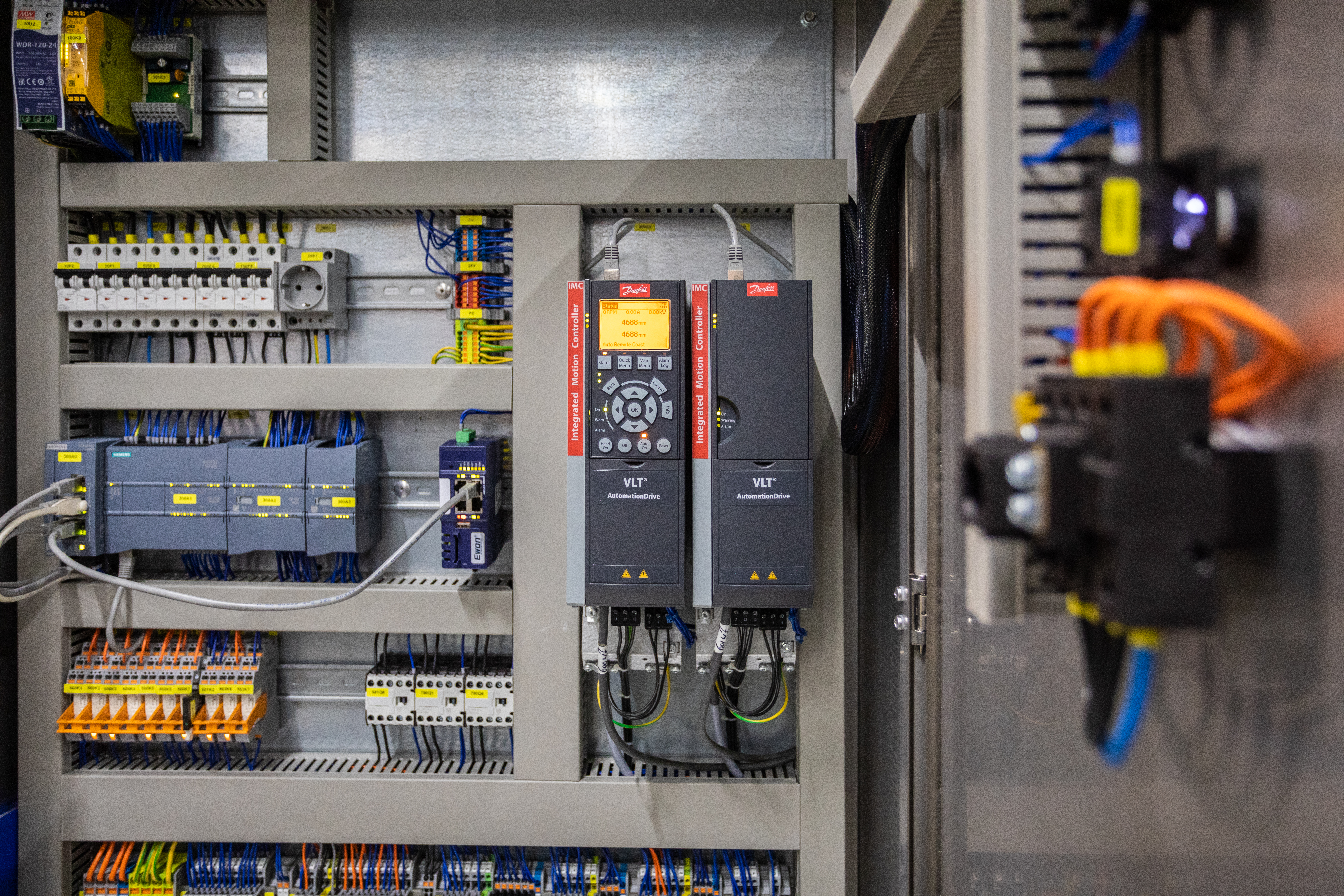
Traditionally, servo drives have been used for these types of positioning and synchronization operations — an expensive, complex, and often unreliable solution. By contrast, the VLT® AutomationDrive FC 302 with its IMC functionality is much cheaper and more robust. It is also easier to use, maintain and adjust. All this with only a fractional reduction in dynamic performance compared to servo technology.
IMC is an innovative alternative to servo control. Essentially, IMC is software functionality that enables an AC drive to perform high-precision positioning and synchronization operations without the need for additional modules or hardware. It is also configured via parameters for easier, faster, safer, and cheaper set-up — there is no need for advanced programming or servo technology knowledge.
With the Danfoss VLT® AutomationDrive FC 302, Huwa’s fully automated pickling line features high-precision positioning and synchronization with minimal complexity and at a fraction of the cost of conventional alternatives. Huwa is already enjoying reduced maintenance costs and fast ROI, thanks to these drives from Danfoss.
Louis Van Der Kaaden, Partner Support Engineer at Danfoss Drives
The outcome: Maximum uptime and rapid ROI
Since September 2021, Huwa’s fully automated pickling line has been 100 percent reliable. With its IMC functionality, the Danfoss VLT® AutomationDrive FC 302 has achieved much faster lead times, while Danfoss’ overall support has been described as “top notch”.
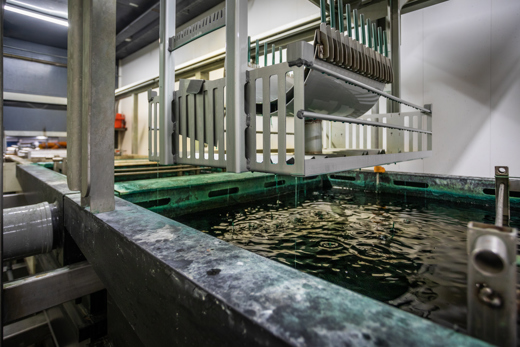
The Danfoss VLT® AutomationDrive FC 302 has also proven itself to be highly adaptable. New movement profiles for the gantry crane are calculated quickly and executed seamlessly. Combining this with maximum uptime thanks to the Danfoss VLT® AutomationDrive FC 302’s robust construction, Huwa’s pickling line is no longer a bottleneck in its manufacturing process.
Benefits of Integrated Motion Controller (IMC) functionality:
- Compatible with all conventional motor technologies, with closed loop and open loop control
- Lower purchase cost due to fewer components
- Reduced electrical and mechanical installation time and cost
- No advanced programming or servo technology knowledge required — minimizes risk of errors in set-up
- Sensor-less homing with torque detection
- Reduced maintenance costs — maximum uptime
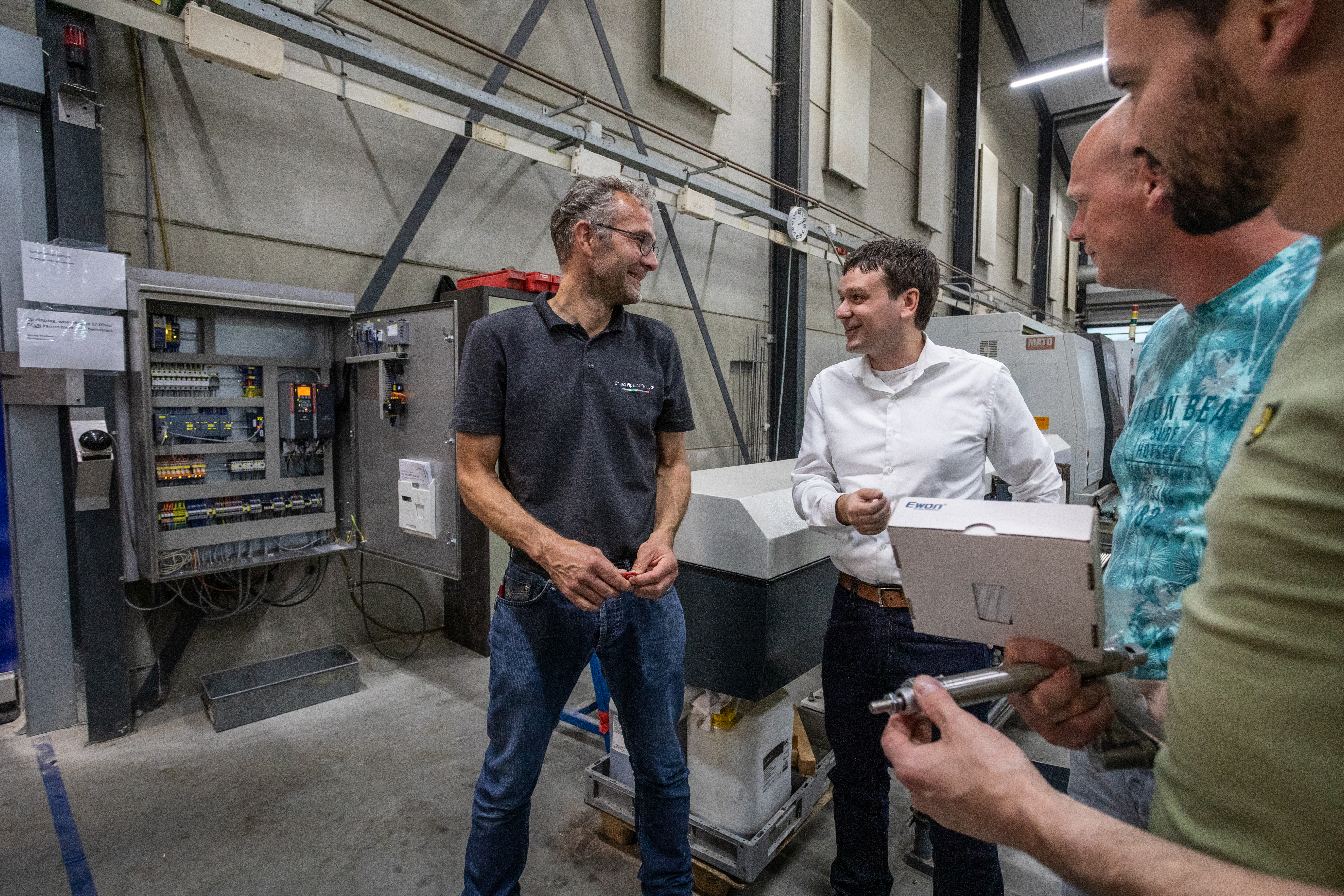
Curious to learn more about Integrated Motion Controller?
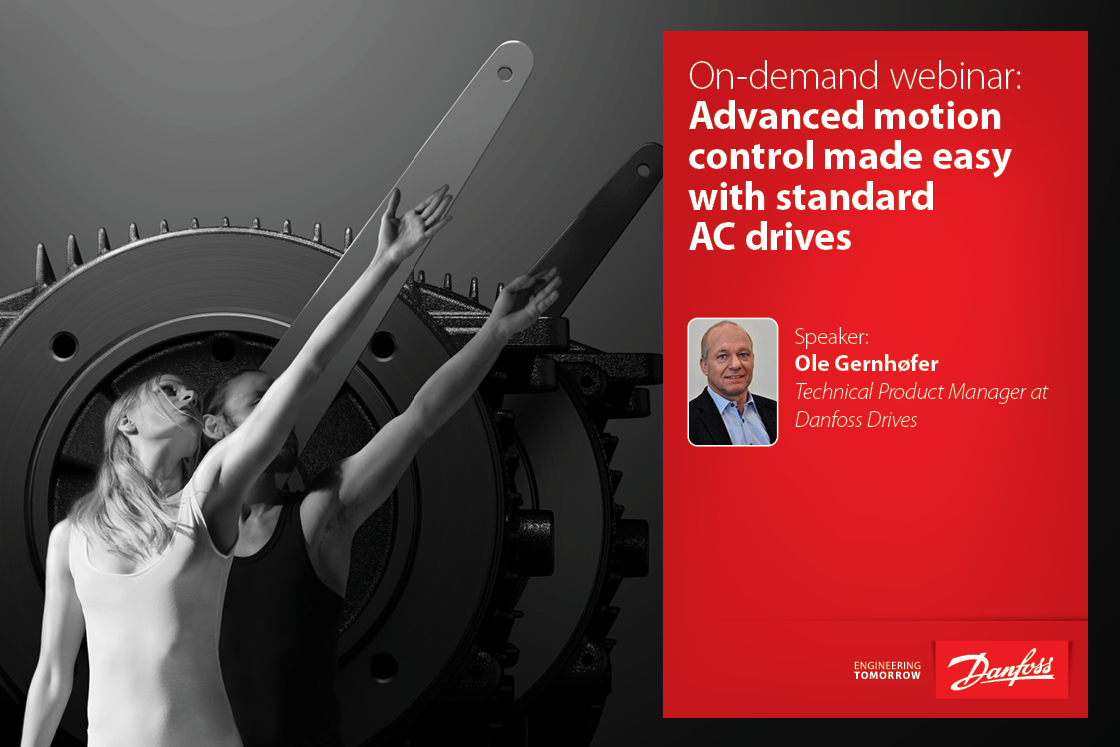
SourceDanfoss
EMR Analysis
More information on Danfoss: See the full profile on EMR Executive Services
More information on Kim Fausing (President and CEO, Danfoss): See the full profile on EMR Executive Services
More information on Danfoss Drives: https://www.danfoss.com/en/about-danfoss/our-businesses/drives/about-danfoss-drives/ + Danfoss Drives is a global leader in AC/DC and DC/DC power conversion, as well as variable speed control for electric motors. With the world’s largest portfolio of power converters, VLT® drives, and VACON® drives at your fingertips – and backing from a partner whose legacy has been built on decades of passion and experience – your journey to a better future is only just beginning.
More information on Mika Kulju (Member of the Group Executive Team, President Danfoss Drives, Danfoss): See the full profile on EMR Executive Services
More information on Louis Van Der Kaaden (Partner Support Engineer, Danfoss Drives, Danfoss): See the full profile on EMR Executive Services
More information on Michael Kannekens (Application Engineer, Danfoss Netherlands, Danfoss): See the full profile on EMR Executive Services
More information on Integrated Motion Controller by Danfoss: https://www.danfoss.com/en-us/about-danfoss/our-businesses/drives/knowledge-center/integrated-motion-controller/ + High-precision positioning and synchronization with reduced costs and system complexity.
Danfoss Drives has developed an innovative alternative to servo control. The Integrated Motion Controller (IMC) is functionality that enables an AC drive to perform high-precision positioning and synchronization operations without the need for additional modules or hardware. IMC is now configurable in the software of the VLT® AutomationDrive FC 302.
IMC has many advantages. It works with all conventional motor technologies, with closed loop or open loop control, and offers sensorless homing with torque detection. Drives are adapted to the applications through simple parameterization. This means that knowledge of servo technology or programming languages is not required. As no encoder or additional cables are needed, engineering, installation and commissioning time and costs can be reduced.
More information on VLT® Drives by Danfoss: https://www.danfoss.com/en-us/products/dds/low-voltage-drives/#tab-vlt-drives + The VLT® AutomationDrive is designed for variable speed control of all asynchronous motors and permanent magnet motors. It comes in a standard version (FC 301) and an advanced high dynamic version (FC 302) with additional functionalities.
More information on VLT® AutomationDrive FC 301 / FC 302 by Danfoss: https://www.danfoss.com/en/products/dds/low-voltage-drives/vlt-drives/vlt-automationdrive-fc-301-fc-302/ +
VLT® AutomationDrive takes full advantage of all that the new digital age has to offer to ensure it completely fulfills the requirements of your applications and optimizes your processes throughout the entire lifecycle.
Its cutting-edge thermal design and unique back-channel cooling make VLT® AutomationDrive one of the most compact and cost-efficient drives in the market. Intelligent maintenance and monitoring functions improve the productivity, performance, and uptime of your systems in the long term.
More information on Huwa International Pipeline Products BV: https://huwa.com/ + HUWA international BV is a company which manufacturers the HUWA stainless steel repair clamps in their own plant since the beginning of the 80’s and has become one of the leading manufacturers in its branch.
HUWA international BV supplies only first class materials and is able to manufacture all kind of sizes, outlets, flanges etc.
HUWA international BV is the supplier of the HUWA stainless steel repair clamps, stainless steel internal repair clamps, stainless steel tapping saddles, stainless steel support bushes, etc.
HUWA is part of United Pipeline Products. United Pipeline Products has been the total supplier of stainless steel repair clamps and couplings for over 25 years. The modern factory and central office is located in the province of Noord Brabant in the town of Sint Oedenrode. With more than 50 employees we manufacture from this location reliably providing unique products for many industries around the world.
The United Pipeline Products holding consists of the following companies:
- HUWA International Pipeline Products B.V.
- Romacon Petro B.V.
- Romacon Pipeline Products B.V.
- UNI-Coupling B.V.
- Gekave International B.V.
- Hegawa B.V.
More information on Twan Van Heesch (Managing Director and Co-owner, Huwa International Pipeline Products): https://www.linkedin.com/in/twanvanheesch/
More information on ISO: http://www.iso.org/ + ISO (International Organization for Standardization) is the world’s largest developer of International Standards. Through our members and their stakeholders, we bring people together to create International Standards that respond to global challenges. ISO standards support global trade, drive inclusive and equitable economic growth, advance innovation and promote health and safety to achieve a sustainable future. Follow us to learn more about standards and how you can participate to making lives easier, safer, and better.
More information on ISO 45001 (OH&S): https://www.iso.org/standard/63787.html + Occupational health and safety management systems — Requirements with guidance for use.
ISO 45001:2018 specifies requirements for an occupational health and safety (OH&S) management system, and gives guidance for its use, to enable organizations to provide safe and healthy workplaces by preventing work-related injury and ill health, as well as by proactively improving its OH&S performance.
ISO 45001:2018 is applicable to any organization that wishes to establish, implement and maintain an OH&S management system to improve occupational health and safety, eliminate hazards and minimize OH&S risks (including system deficiencies), take advantage of OH&S opportunities, and address OH&S management system nonconformities associated with its activities.
More information on Hellings Machinebouw: https://hellingsmachinebouw.nl/en + Hellings Machinebouw has over 30 years of experience in the food industry. The Hellings Machinebouw & Engineering team is constantly engaged in the design, manufacture and installation of machines and production lines, specifically finding use in the primary treatment, processing and packaging of food.
After having operated under the name Advies & Constructiebureau Bakermans B.V. for nearly 9 years, the name Hellings Machinebouw & Engineering has been in place since 2001. Huge success led to the company becoming an established name. Since June 2006 Hellings has been located in Nijnsel (municipality of Sint-Oedenrode), where all design, manufacturing and assembly of the machines takes place.
We aim to be the preferred supplier for OEM and end-users over the entire world focusing on the areas of internal transport, handling and packaging solutions, as well as custom machinery. All for use in the food industry.
More information on Harm van der Pol (Managing Director, Hellings Machinebouw): https://www.linkedin.com/in/harm-van-der-pol-02997b7/
More information on Sonepar: See the full profile on EMR Executive Services
More information on Philippe Delpech (CEO, Sonepar): See the full profile on EMR Executive Services
More information on Sonepar Nederland:
- Technische Unie: https://www.technischeunie.nl + Technische Unie is a leader in the B2B electrical distribution market in the Netherlands.
- Engineering is a PROFESSION, in capital letters. Technische Unie enables professionals, who are building our future day in and day out, to do this efficiently and well-informed. With around 2,000 employees of Technische Unie, who are there for you. With a wide range of 2 million article numbers. With services that help you get ahead every day. And with subject-oriented courses from TU Campus.
- Technische Unie is the largest technical wholesaler in the Netherlands. We are your partner for the delivery of installation materials in the field of electrical engineering, light, tools, (luxury) plumbing, heating and climate technology. Our customers are active in the installation sector (housing or utility), construction, industry, (semi) government and retail.
- Technische Unie is a wholesaler of technical solutions for installation and industry. In the Netherlands there are 41 branches (sales offices, points of sale and pick-up points), 2 distribution centers in Alphen aan den Rijn and Strijen, and 1 Central Office in Amstelveen.
- Van Egmond Group: https://www.vanegmond.nl + Van Egmond Group provides products and services in the fields of electrical engineering and industrial automation.
- Our goal is to provide each customer with the best possible solution. Personal contact, quality and reliability are the key drivers within our company. From this philosophy, Van Egmond Groep has been advising and servicing its relations in the industry (MRO) and machine- and panel builders (OEM) for over 80 years with a wide range of products, services and official dealerships. Our Industrial Automation division is active in all sectors of the industry. Industrial service, Software Engineering, Hardware Engineering and assembly of power distribution panels are the core activities. Complemented by our education branch, we offer our industrial customers a full service package. Van Egmond is your partner for electro technology and industrial service.
- Van Egmond Group consists of three companies, namely: Electrical Wholesale, Industrial Automation and Knowledge Center.
- Electrical wholesale: We are more than a wholesaler. In addition to supplying products and systems, we also offer advice. We are your knowledge partner from design to delivery, installation, commissioning and maintenance. We are available 24 hours a day for this. We also provide services and options in the field of efficient engineering, e-business and customized logistics.
- Industrial automation: We are active in the field of industrial services in all sectors. Software Engineering, hardware engineering and the construction of low-voltage power distribution boards are the core activities as a total supplier for machine builders, the self-installing industry and installers.
- Knowledge center: Van Egmond Groep offers two types of training: regular training and customized training. We are your partner to offer or develop the most suitable learning experience. Our knowledge center is also involved in R&D activities and develops various tools that are in line with the rapidly changing and increasingly demanding market
- UBEL: https://ubel.nl/home + Ubel is a partner of choice for equipment for large-scale plumbing installations in the Netherlands.
- Ubel is a specialist in valves and appendages and therefore the partner for large installers in the non-residential construction industry. Our range includes products for the entire distribution channel. You can also count on expert advice for your specific situation. Ubel’s technical knowledge extends from hydraulic balance to legionella prevention and from underfloor heating to steam and condensate installations. Ubel is based in Hengelo, but our roots are in the British industrial city of Manchester, where Ubel started under the name United Brassfounders Engineers Limited. In 1921 we became active on the Dutch market and since 1945 our focus has been on large W installations for non-residential construction. We have been part of Technische Unie since 2013 and are active throughout the Netherlands.
More information on Jan Ferwerda (CEO Sonepar Nederland/Technische Unie): See the full profile on EMR Executive Services
EMR Additional Notes:
- PLC (Programmable Logic Controller):
- Programmable Logic Controllers (PLCs) are industrial computers, with various inputs and outputs, used to control and monitor industrial equipment based on custom programming.
- Receive information from input devices or sensors, process the data, and perform specific tasks or output specific information based on pre-programmed parameters. PLCs are often used to do things like monitor machine productivity, track operating temperatures, and automatically stop or start processes. They are also often used to trigger alarms if a machine malfunctions.
- A PLC takes in inputs, whether from automated data capture points or from human input points such as switches or buttons. Based on its programming, the PLC then decides whether or not to change the output. A PLC’s outputs can control a huge variety of equipment, including motors, solenoid valves, lights, switchgear, safety shut-offs and many others.
- PLC can be used for motion control, but with difficult programming and complexity; whereas a motion controller can be used for process automation too with equal easiness.
- A PLC is a stand-alone unit that can control one or more machines and is connected to them by cables. On the other hand, in an embedded control architecture the controller — which is almost always a printed circuit board (PCB) — is located inside the machine it controls.
- Motion Control:
- Process of moving machinery using rotary and linear actuators. Motion Control is a sub-field of automation whereby position or velocity machines are controlled using a motion control device, such as a linear actuator, electric motor, a hydraulic pump or a servo motor.
- Motion controllers are special devices that control the engine operating modes. In other words, it’s the brain of every motion control system. As such, its task is telling the motor what to do based on the desired production outcome.
- Motion control means “to control movement.” One distinctive example is positioning control by various motors. By giving electronic energy to a motor, a motor operates and converts it to motional energy.